Rubber waste management – common misconceptions explained
Rubber waste management has long been a thorny issue in Europe’s sustainability goals. From tires discarded in fields to bulky industrial scraps ending up in landfills, managing rubber-based materials is both an environmental challenge and an economic opportunity. As regulatory pressure grows and circular economy targets tighten, the question isn’t whether we should recycle rubber waste—but how to do it right. This article explains the scope of the issue, the complexities in defining and treating rubber waste, and how modern recycling methods and policy shifts are reshaping the industry.
Do you need help with waste management? Contact us:
Understanding rubber waste: what it is and why it matters
Rubber waste types by industry and material composition
Rubber waste in Europe comes from various economic sectors, each generating materials with different properties and recycling challenges:
End-of‑life tires (ELTs)
- Origin: Passenger vehicles, trucks, agricultural and industrial machinery.
- Scale: Around 3.4 million tonnes of ELTs are collected yearly in the EU—approximately 95 % of tires produced.
- Composition: Mostly vulcanized rubber and steel belts, often used in road building, playgrounds, or cement kilns.
Industrial rubber products
- Origin: Hoses, conveyor belts, seals, gaskets used in manufactured goods.
- Composition: Diverse—can include natural rubber, synthetic variants like nitrile or EPDM, composites, and metal reinforcement.
Automotive shredder residue (ASR)
- Origin: Shredded end‑of‑life vehicles after initial reuse.
- Composition: A mix of rubber, plastic, glass, and metal. ASR is difficult to separate and often considered hazardous or difficult-to-handle waste
Consumer rubber waste
- Origin: Items such as hoses, footwear soles, mats, or rubber toys.
- Composition: Often rubber-plastic composites or soiled/ragged materials from household sources.
Why rubber waste classification matters—and where it often fails
Rubber ≠ plastic
Properly distinguishing rubber waste from plastic is fundamental—not just for selecting appropriate recycling methods, but also for staying within regulatory bounds. Yet this seemingly straightforward task is often fraught with confusion. A major source of misidentification stems from the vulcanization process. Through sulfur cross-linking, rubber acquires its signature elasticity and durability, but this also makes it chemically and physically distinct from thermoplastics. Despite visual similarities, vulcanized rubber does not behave like plastic—it resists melting, reprocessing, and degradation in entirely different ways.
Consequences of misunderstanding
This misunderstanding leads to tangible consequences. Data shows that only around 40% of rubber waste is correctly identified as reusable. The remainder is often mishandled—diverted to incineration or landfills, or worse, fed into inappropriate recycling streams. In some cases, mistaking rubber for plastic—such as processing end-of-life tires in shredders meant for plastic—can release fine rubber dust or heavy metals into the air, posing risks to both human health and the environment. Administrative errors are also common: when rubber waste is misclassified on shipment documents, it can trigger serious compliance issues under transboundary waste regulations.
The vulcanization dilemma: strength vs. sustainability
The heart of the problem lies in rubber’s very strength—its resistance to degradation. Vulcanization, which makes rubber so reliable in use, also makes it notoriously difficult to recycle. Unlike plastics that can often be melted down and remolded, rubber requires energy-intensive processes to break down its molecular structure, which complicates both material recovery and economic feasibility.ed with bulkiness, transport difficulties, and a lack of dedicated treatment plants, the economic feasibility of rubber recycling remains a challenge.
Can rubber waste be recycled? Treatment technologies that make it possible
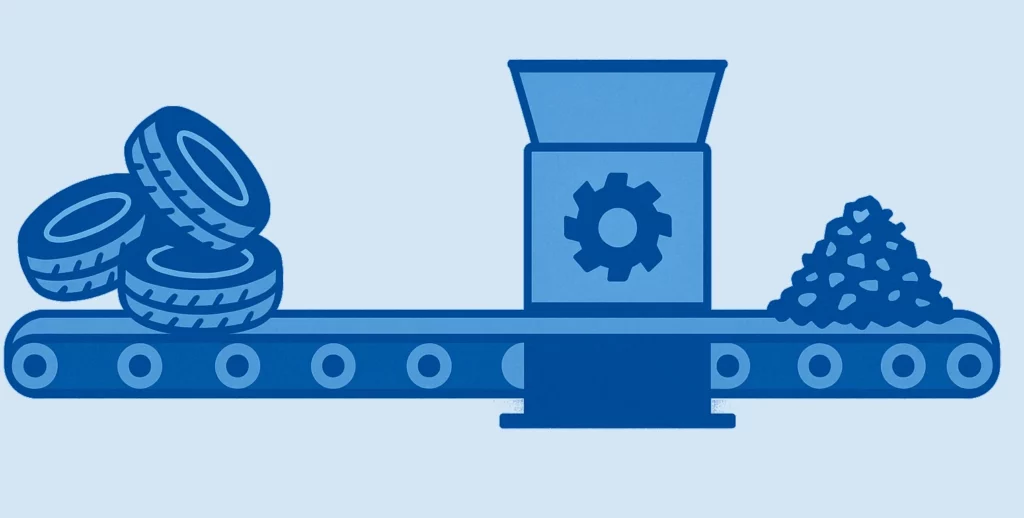
Mechanical recycling (most common)
This involves shredding and grinding rubber into crumb rubber, which can be repurposed in:
- Artificial turf and playground surfaces
- Rubberized asphalt for roads
- Shock-absorbent mats
While mechanically recycled rubber has limited applications due to material degradation, it remains the most widely adopted method.
Devulcanization
A more advanced technique that involves breaking the sulfur cross-links in vulcanized rubber to restore plasticity. It can create materials usable in new rubber products but suffers from:
- Inconsistent output quality
- High energy demands
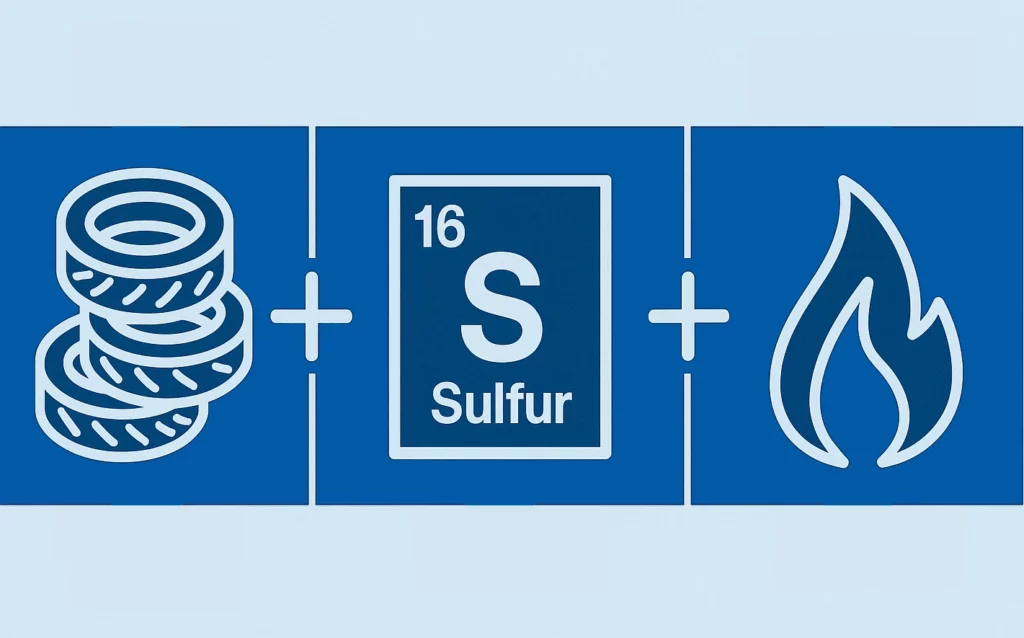
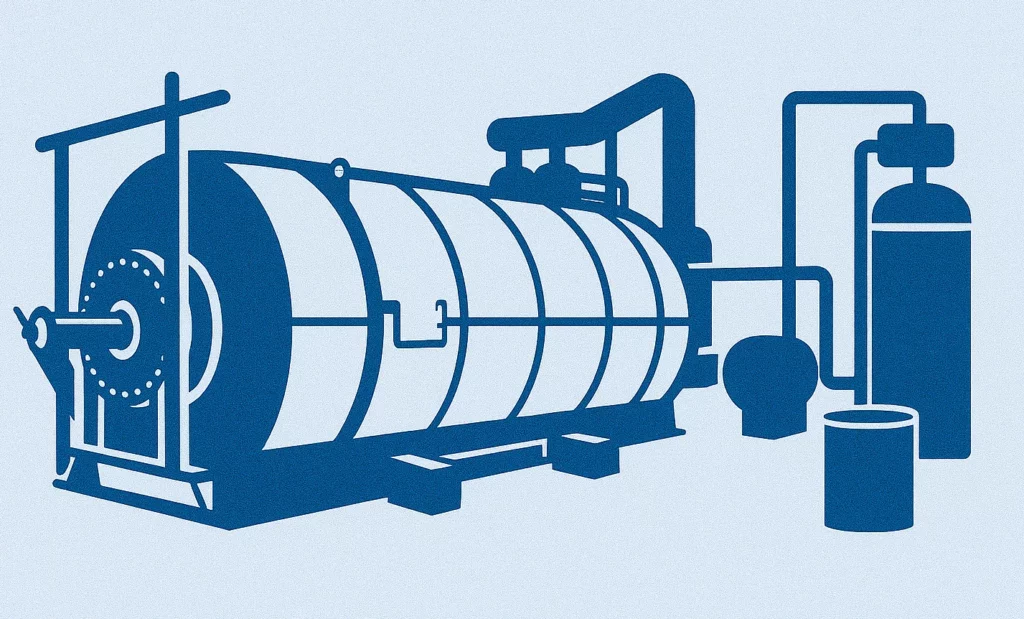
Pyrolysis
Thermal decomposition in an oxygen-free environment yields:
- Gas (for energy use)
- Oil (as industrial fuel)
- Carbon black (a material for tire manufacturing)
However, pyrolysis faces cost and regulatory hurdles, particularly regarding emissions (PAH – Polycyclic Aromatic Hydrocarbons, which are by-products of incomplete combustion, and dioxins – highly toxic environmental pollutants).
Last resort – co-processing in cement kilns
Here, shredded tires are given second chance as alternative fuel in cement production. Though it doesn’t recycle the material, it reduces fossil fuel use. The downside? It eliminates the possibility of reusing the rubber as a material. That’s why it is primarily considered a last-resort solution—used when other technologies prove ineffective or when the demand for such fuel outweighs the benefits of alternative methods.
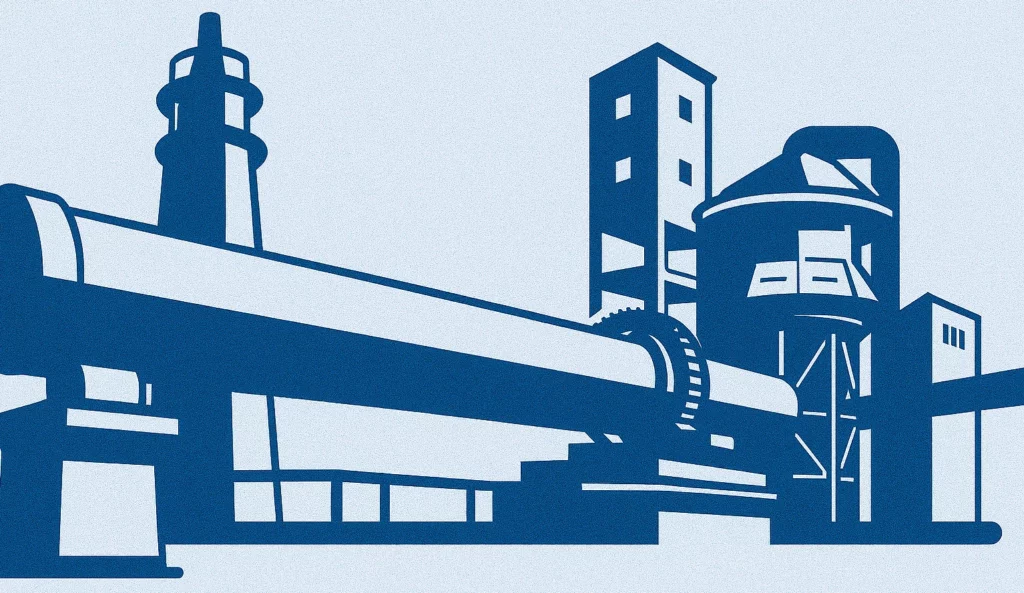
EU regulations shaping rubber waste management
The foundation: Waste Framework Directive
The EU’s main waste law, the Waste Framework Directive, sets the overall rules for how waste should be handled. It introduces the waste hierarchy, which means waste should first be prevented, then reused, recycled, recovered, and only as a last resort—disposed of. It also brings in the idea of Extended Producer Responsibility (EPR), making producers and importers responsible for what happens to their products after use, including tyres. Another important feature is the end-of-waste rule, which explains when a material stops being waste and becomes a resource again. Rubber waste, including end-of-life tyres (ELTs), is covered under this law—unless more specific rules apply.
Cross-border movement: Waste Shipment Regulation
If rubber waste is moved between countries, the Waste Shipment Regulation applies. It ensures that shipments—especially those meant for recycling or recovery—are properly tracked and reported. ELTs not meant for direct reuse are usually put on the “amber list”, which requires notification procedures before transport. This law helps prevent illegal dumping and ensures waste ends up in facilities that can handle it safely.
What’s allowed in landfills: Landfill Directive
Under the Landfill Directive, dumping rubber waste is heavily restricted. Whole tyres have been banned from landfill since 2006, and shredded ones since 2003 (with a few exceptions). This has pushed the market toward better options, like recycling, pyrolysis, and energy recovery in industrial facilities.
National tyre rules: ELT management and circular economy
Although there’s no EU law just for ELTs, many countries run national EPR schemes for tyres under the Waste Framework Directive. These schemes make tyre producers pay for collection and recycling. The Circular Economy Action Plan from the EU also supports better design of products and improved use of recycled materials, including rubber. It encourages innovation, such as devulcanization, which helps turn used rubber into new raw material.
Chemical safety: REACH Regulation
The REACH Regulation is not about waste, but it still affects rubber recycling. That’s because recycled tyre granules used in playgrounds and sports fields must meet strict limits for harmful substances, like PAHs (carcinogenic, mutagenic by-products of incomplete combustion) and heavy metals. New EU rules about microplastics—including rubber particles—are also coming, and they’ll affect where and how rubber granulate can be used.
Emissions control: Industrial Emissions Directive
Rubber waste that’s burned or chemically treated must follow the Industrial Emissions Directive. This includes incineration, co-incineration in cement kilns, or pyrolysis. Facilities handling these processes must stick to strict emissions limits and use the BAT – Best Available Techniques (for preventing or minimising emissions and impacts on the environment) to protect the environment and human health.
What’s holding rubber waste management back?
- Logistical constraints: Rubber waste is bulky and expensive to store and move. Remote areas often lack access to nearby recycling plants.
- Economic viability: Virgin rubber remains cheaper in many cases, limiting the demand for recycled alternatives.
- Environmental risks: Improperly stored tires can become breeding grounds for mosquitoes or catch fire, releasing hazardous compounds.
- Regulatory inconsistency: Disparities in rubber waste classification and enforcement weaken Europe’s unified recycling strategy.
- Market limitations: Even after successful recycling, end-market demand for recycled rubber remains restricted, with many sectors still preferring virgin material.
Turning policy into progress: what Europe must do next
To translate policy into measurable progress, Europe must shift from fragmented initiatives to coordinated action that delivers both environmental and economic value. A critical starting point lies in accelerating investments in advanced recovery technologies—particularly devulcanization and chemical recycling. These processes, once confined to laboratory interest, are now maturing into industrially viable methods capable of producing high-quality rubber compounds at competitive prices. Supporting their scalability could fundamentally reshape the market for secondary raw materials.
However, innovation alone won’t suffice without regulatory alignment. A unified EU approach to tire classification and end-of-waste criteria is long overdue. Inconsistent interpretations across member states not only hinder cross-border cooperation but also leave recyclers and manufacturers operating in legal uncertainty. Streamlining policy at the European level would create predictability and boost investor confidence.
Equally important is the need for research into clean pyrolysis technologies. Traditional systems often grapple with emissions of PAHs and dioxins, drawing scrutiny and regulatory resistance. Emerging solutions—designed with integrated emissions controls—could help rehabilitate pyrolysis as a credible option for rubber waste valorization rather than a last resort.
Finally, the logistical footprint of rubber waste management must be addressed. Expanding regional recycling centers, particularly near major tire consumption zones, would drastically cut down on transport emissions and costs. It would also support circular economy principles by keeping material flows localized and resilient.
How Waste Transport Solutions can help
At Waste Transport Solutions, we understand that rubber waste management is as much about logistics and compliance as it is about sustainability. As part of Ekologistyka24 Group, we bring over a decade of cross-border expertise to help you manage your rubber waste properly.
We offer:
- End-to-end transport solutions across the EU for rubber waste.
- Assistance with documentation under EU law.
- Access to certified recyclers using mechanical, thermal, and emerging technologies.
Rubber waste is not just a challenge—it’s a resource worth recovering. Let us help you make the transition from landfill to lifecycle.